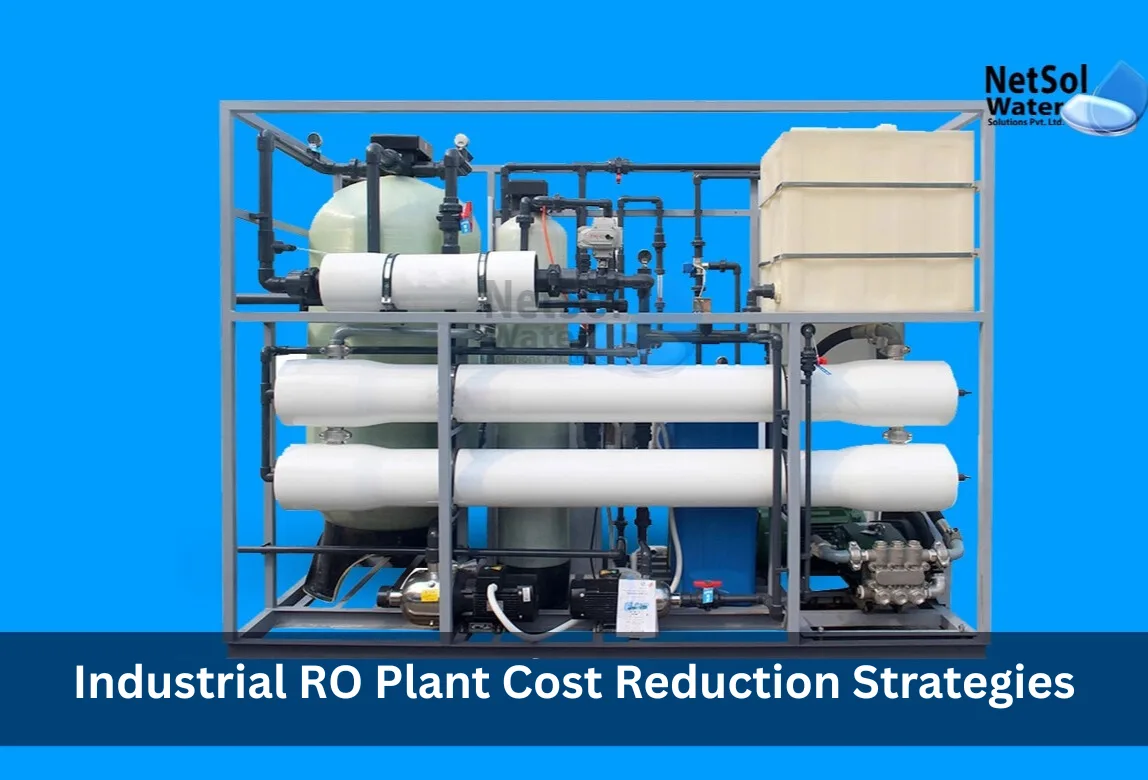
Industrial RO Plant Cost Reduction Strategies
Water treatment plays a central role in industrial operations. Many businesses spend substantial money on reverse osmosis (RO) plants to ensure clean water for their processes. The growing focus on sustainability pushes industries to find better ways to manage their RO systems. Water quality parameters serve as key indicators that help industries optimize their RO plant operations. By understanding these parameters businesses can make informed decisions about their water treatment processes. This knowledge leads to significant cost savings without compromising water quality standards. The following section explores practical strategies to reduce industrial RO plant costs through effective monitoring of water quality parameters. These approaches help businesses maintain high water quality while keeping operational expenses in check.
Water Quality Parameters for Cost Optimization
Water quality parameters form the foundation of efficient RO plant operation. These measurements tell us about water characteristics that affect the RO system performance. Different industries need different water quality levels based on their specific processes. A food processing plant needs different water standards compared to a power generation facility. By tracking these parameters plant operators can spot issues before they become expensive problems. This proactive approach prevents unnecessary maintenance costs.
Let us look at the key parameters that impact RO plant costs:
- Total Dissolved Solids (TDS): TDS monitoring helps predict membrane fouling rates. High TDS levels mean more frequent membrane cleaning or replacement. Regular TDS checks allow operators to adjust pretreatment processes. This adjustment extends membrane life which saves money on replacements.
- pH Levels: The pH value affects membrane performance. Improper pH leads to scaling or chemical damage. Maintaining optimal pH reduces chemical usage. It also prevents unexpected shutdowns that increase operational costs.
- Turbidity: Turbidity indicates suspended particle content. High turbidity causes faster membrane clogging. Monitoring helps optimize filtration processes. Better filtration means longer membrane life spans.
- Conductivity: Conductivity measurements show dissolved ion concentrations. These readings help operators adjust chemical dosing. Proper dosing prevents wastage of expensive treatment chemicals.
Pretreatment Optimization for Cost Reduction
Pretreatment systems protect RO membranes from damage. Good pretreatment extends membrane life which reduces replacement costs. It also lowers energy consumption because clean membranes work more efficiently. This section explores ways to enhance pretreatment effectiveness.
Let us examine the main pretreatment optimization strategies:
A. Multimedia Filtration Enhancement: Multimedia filters remove suspended solids. Regular backwashing prevents filter media deterioration. Proper maintenance schedules save money on media replacement. It also ensures consistent water quality entering the RO system.
B. Chemical Dosing Control: Smart chemical dosing prevents scaling. Automated systems adjust chemical levels based on water quality. This precision prevents chemical waste. It also protects membranes from chemical damage.
C. Antiscalant Selection: The right antiscalant prevents mineral deposits. Different water sources need different antiscalants. Proper selection reduces cleaning frequency. It also prevents permanent membrane damage.
D. Carbon Filter Management: Carbon filters remove organic compounds. Regular carbon media replacement maintains effectiveness. This consistency prevents organic fouling. It also reduces membrane cleaning requirements.
Operational Efficiency Improvements
Operational efficiency directly affects RO plant costs. Small improvements add up to significant savings. This section focuses on practical ways to enhance daily operations. These strategies help maintain optimal performance while reducing expenses.
Let us explore key operational improvements:
- Energy Usage Optimization: High-pressure pumps consume most RO plant energy. Variable frequency drives adjust pump speed based on demand. This adjustment reduces unnecessary energy use. Proper pressure management also prevents membrane damage.
- Membrane Cleaning Schedules: Timely membrane cleaning prevents performance loss. Regular monitoring helps plan cleaning cycles. This planning reduces chemical use. It also prevents emergency maintenance needs.
- Data Monitoring Systems: Modern monitoring systems track performance metrics. Real-time data helps operators make quick decisions. This responsiveness prevents costly breakdowns. It also optimizes chemical and energy use.
- Staff Training Programs: Well-trained operators run plants more efficiently. Regular training updates technical knowledge. This expertise prevents operational mistakes. It also improves maintenance effectiveness.
Take Action for Better Water treatment:
Want to reduce your industrial RO plant costs through better water quality management? Our team specializes in water quality parameter optimization. Contact us today for a detailed assessment of your RO system. We will show you practical ways to save money while maintaining excellent water quality. Book a consultation now to start your cost-reduction journey.
To explore customised commercial RO plants, Industrial RO plant, ETP or STP solutions for your needs in your areas and nearby regions, Contact Netsol Water at:
Phone: +91-965-060-8473
Email: enquiry@netsolwater.com