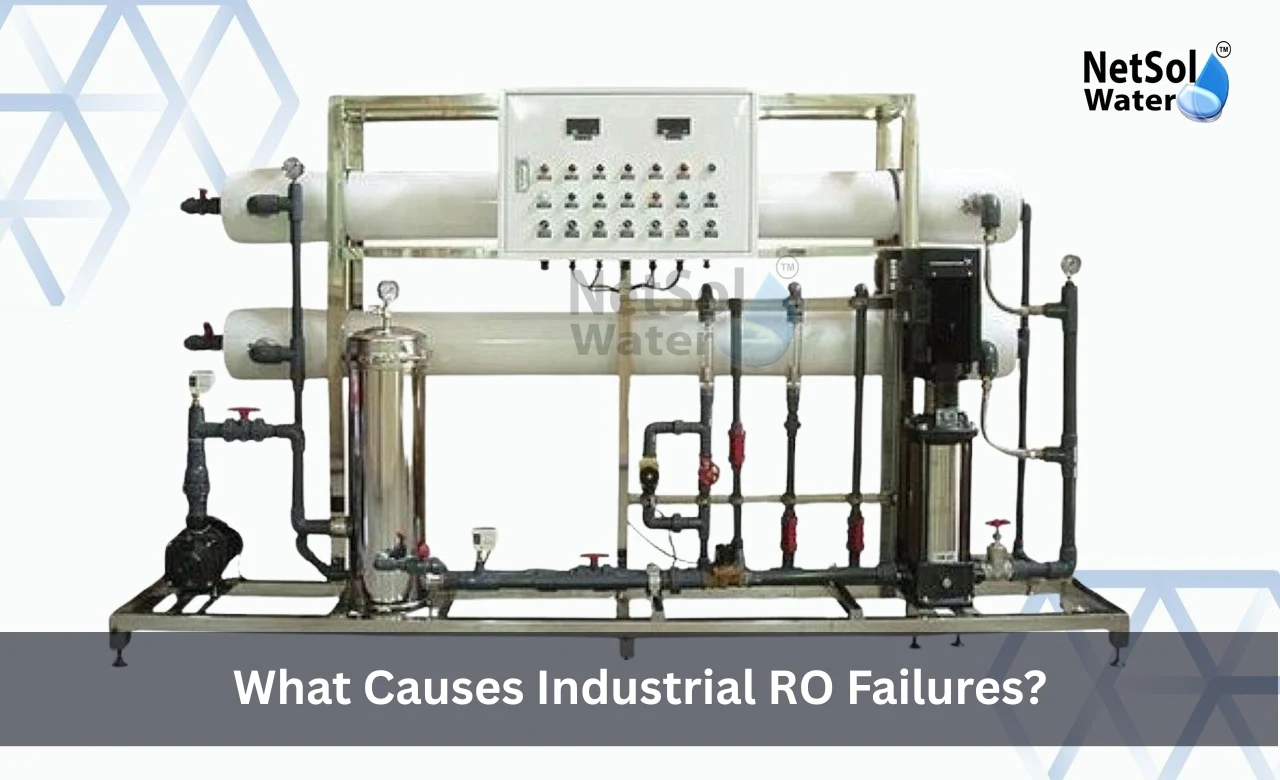
What Causes Industrial RO Failures?
Industrial RO Plant serve as the backbone of water treatment across many industries. These systems transform untreated water into pure water by pushing it through specialized membranes. Yet many businesses face unexpected shutdowns because their RO systems fail. This creates serious problems for production schedules and increases operational costs. Understanding why industrial RO systems fail helps plant managers take the right steps to prevent issues before they happen.
The impact of RO failures extends beyond just lost production time. When an industrial RO system stops working companies must spend money on emergency repairs. They also risk making products that don’t meet quality standards. This affects everything from pharmaceutical manufacturing to food processing. Plant operators need to understand common failure causes so they can spot warning signs early. This knowledge enables them to take action before small issues become big problems.
Poor Maintenance Practices Lead to System Deterioration
Maintenance forms the foundation of RO system health. Many industrial RO failures start with inadequate maintenance routines. Proper system upkeep involves more than just occasional cleaning. It requires careful monitoring regular part replacement and proper documentation of all maintenance activities. Let’s examine how different maintenance oversights contribute to system failure:
1. Inconsistent Membrane Cleaning: RO membranes need regular cleaning to work properly. Scale biofilm and other deposits build up over time on membrane surfaces. This buildup creates pressure drops across the system. The result is decreased water flow and higher energy usage. Operators must follow manufacturer cleaning schedules. They should also adjust cleaning frequency based on feed water quality.
2. Delayed Parts Replacement: Every component in an RO system has a specific lifespan. Cartridge filters membrane elements and other parts degrade over time. Using worn-out parts strains the entire system. This leads to poor performance and eventual failure. Keeping detailed records of installation dates helps plan timely replacements.
3. Insufficient Monitoring: Daily system monitoring catches small issues before they become serious problems. Operators should track pressure readings flow rates and water quality parameters. Changes in these measurements often signal developing problems. Creating clear monitoring procedures helps operators identify concerning trends.
Feed Water Quality Issues Create System Stress
The quality of water entering an RO system directly impacts its performance. Many industrial RO failures stem from feed water problems. Understanding how different water quality issues affect system components helps prevent damage. Let’s explore the major feed water factors that cause RO failures:
- High Sediment Load: Excessive particles in feed water clog pre-filters and membranes. This creates uneven pressure across the system. The extra strain damages membrane fibers and reduces system efficiency. Installing proper pre-treatment equipment protects downstream components.
- Chemical Contamination: Industrial feed water often contains harsh chemicals. These substances can break down membrane materials. Chlorine organic compounds and heavy metals pose special risks. Testing feed water regularly helps identify harmful substances before damage occurs.
- Temperature Variations: Sudden changes in feed water temperature stress RO membranes. This leads to membrane cracking and system failure. Installing temperature control equipment helps maintain stable operating conditions. Proper system design accounts for expected temperature ranges.
Operational Errors Damage System Components
How operators run an RO system affects its longevity. Many failures trace back to operational mistakes. Training operators about proper procedures prevents many common errors. Let’s examine key operational factors that lead to system failure:
1. Improper Startup and Shutdown: Starting or stopping an RO system incorrectly stresses components. Rapid pressure changes can damage membranes and seals. Following proper procedures for each startup and shutdown protects the system. This includes flushing lines and gradually adjusting pressures.
2. Incorrect Operating Parameters: Running an RO system outside design specifications causes damage. Pressure flow rate and recovery must stay within acceptable ranges. Operators need clear guidelines about proper operating conditions. Regular training reinforces correct operational practices.
3. Poor Record Keeping: Incomplete records make it hard to spot developing problems. Operators should document all system changes and maintenance work. This information helps troubleshoot issues and plan maintenance. Good records also guide future operational decisions.
Take Action to Prevent Industrial RO Failures
Don’t let RO system failures disrupt your operations. Our team of water treatment experts can help evaluate your system. We identify potential problems before they cause shutdowns. Contact us today to schedule a comprehensive RO system assessment. Learn how to protect your investment and maintain consistent water quality. Our specialists will create a customized plan to keep your industrial RO system running at peak performance.
Contact Sewage Treatment Plant at:
Phone: +91-965-060-8473
Email: enquiry@netsolwater.com